Novel Coronavirus dual-function mask that can be activated and reused is officially put into production in Hefei.
Since the outbreak of the new champions league masks become our important protection tools, also gradually become the necessities of our lives, but ordinary disposable masks protective performance is poor, not only routine surgical masks or KN95 masks are physical blocks to be inactivated virus, scientists have confirmed that are blocked by virus can survive the longest 7 days on the mask, these viruses trapped on the mask may once again become a source of infection, easy to bring secondary pollution, the inactivated will be coronavirus masks, what changes to our daily protection will bring what?
Rolling, cutting, nose strap, ear strap...In the workshop of Anhui Box Health Technology Co., LTD., new KN95 masks are rapidly shaped as the production line rolls along.They will be sold all over the world for 12 yuan each.At present, 10 million are produced and sold every month.
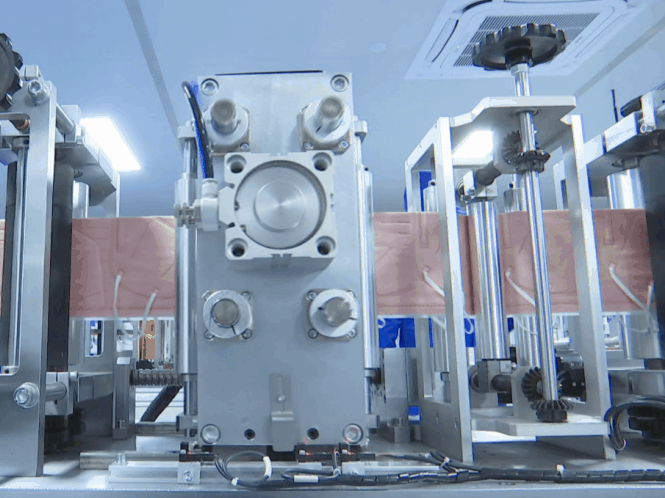
This special mask developed for novel Coronavirus prevention and control uses copper-oxide spunbonded non-woven fabric as the main material and has the characteristics of microbial inactivation.
"Novel Coronavirus special mask not only has the characteristics of high filtration and strong sterilization, but also solves the serious problem that protective mask cannot be reused and causes waste."Huang Yuhao, chairman of Anhui Box Health Technology Co., said that the wearer of this type of protective mask will not spread the virus through contact with the mask during use, so there is no need for complicated disinfection treatment. The mask can be used many times and maintain normal virus filtration and inactivation.
According to introducing, the inactivation effect that contains cuprous oxide material is taller than common cloth 50-90%.Not only can the mask block and kill pathogens, it can be reused up to 60 times.Even if the mask is exposed to the air for many days, there will be no residual bacteria, which solves the problem that protective masks cannot be reused.
The release of the new KN95 mask means that Box Health has become the first manufacturer in the world to apply copper oxide non-woven fabrics to protective masks, marking a breakthrough in the research, development and production of medical protective masks in China.
In fact, as early as 2009, Professor Kelly R. Bright of The University of Arizona in the United States first tested the inactivation effect of different zeolite on SARS coronavirus, and found that the silver ion and copper ion exchange zeolite powder had anti-SARS coronavirus activity, with the inactivation rate of 1 hour up to 90% and 4 hours over 99%.
It is learned that the natural antibacterial ability of copper metal has been certified by the US Environmental Protection Agency in 2008. In recent years, its antibacterial ability has been promoted and applied in the construction of medical systems and large public facilities in Europe and The United States.At present, the mask has obtained all the tests and registration required for the market at home and abroad.
With the official mass production of new KN95 masks, Anhui Box Health Technology Co., Ltd. can produce 2 million KN95 and medical N95 masks per day, making it the largest manufacturer of high-end masks in Hefei.At present, the company has 250 million orders in hand, and the transaction price will reach more than 1.5 billion yuan!
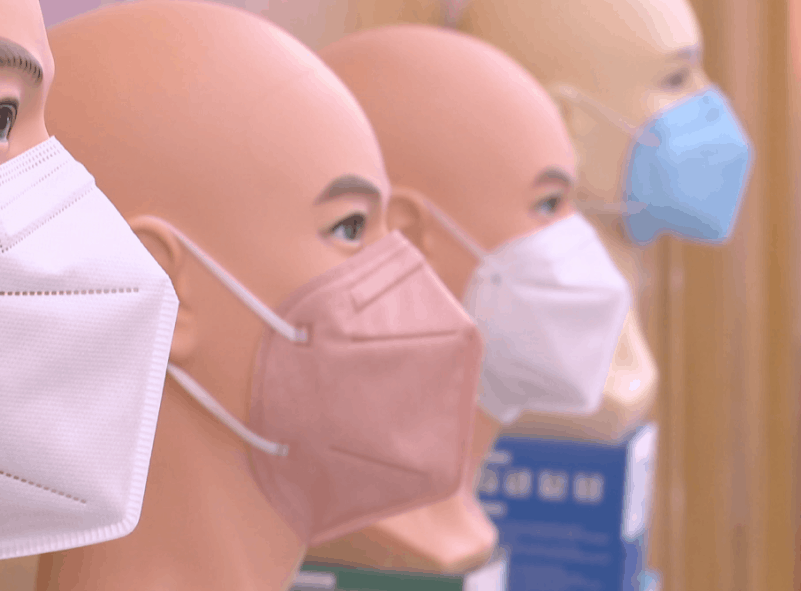
Recently it was reported that CpK Interiors Products Inc., based in Ontario, Canada.A range of antiviral plastics has been developed to eliminate the COVID-19 virus from the material surface within an hour.The company is currently applying for a patent for the plastic.
Dr Gregory Farrar, CpK's head of research and development, said: "This is not an easy task, but our team has had extensive experience in developing novel materials in the past.Not only did CpK have to discover which material could actively attack the DNA of a novel Coronavirus, we also had to comply with strict and timely testing requirements for the new automotive interior material."CpK was able to invent, test, and patent materials within 90 days of launching the program.The team, led by Dr Gregory Farrar, was tasked with developing materials with antiviral properties for automotive interiors.In addition, CpK developed skin casting materials for the Dodge Challenger and Dodge Charger models.
Antiviral testing is another challenge for the company, but CpK has signed a contract with Schulich School of Medicine & Dentistry's ImPaKT facility to perform the tests.
Ted Castle, MANAGING director of CpK, said: "Because the entire supply chain, from raw materials to finished products, is under the same umbrella with CpK, we are able to quickly and quickly invent, test and prototype new materials, an ability that is also critical to the success of antiviral material development programmes."
To sum up, in the face of the COVID-19 epidemic sweeping the world, global researchers have contributed to the epidemic prevention journey, laying a solid foundation for meeting the global demand in the future.